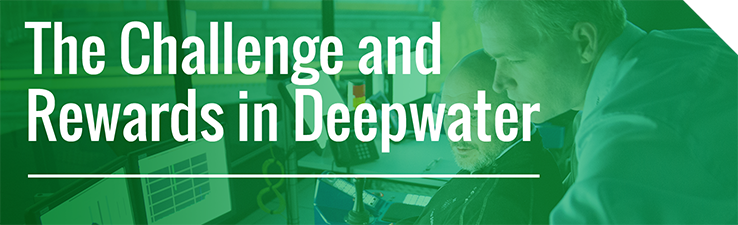
The Challenge and Rewards in Deepwater
Oceans cover just over 70 percent of the Earth's surface and contain 97 percent of the Earth's water. They also contain another valuable resource: Hydrocarbons. Offshore production began in the US in 1896 in the Pacific Ocean offshore California. Modern offshore drilling and production uses equipment and techniques that are as far from those Nineteenth Century platforms as the International Space Station is from the Wright Brothers’ Kitty Hawk airplane.
Since those early milestones, development of sophisticated technology, processes and equipment has enabled the oil and gas industry to expand offshore development, moving into increasingly deeper waters. In this module, you’ll learn about the challenges and rewards of Deep Water Drilling.
A drilling rig is a complex piece of machinery designed for a single purpose — to drill oil, gas or geothermal wells.
Narration Transcript
Oceans cover just over 70 percent of the Earth's surface and contain 97 percent of the Earth's water. They also contain another valuable resource: Hydrocarbons.
Offshore production began in the US in 1896 in the Pacific Ocean offshore California. Modern offshore drilling and production uses equipment and techniques that are as far from those Nineteenth Century platforms as the International Space Station is from the Wright Brothers’ Kitty Hawk airplane.
Since those early milestones, development of sophisticated technology, processes and equipment has enabled the oil and gas industry to expand offshore development, moving into increasingly deeper waters.
A generation ago, deepwater referred to offshore wells in a few hundred feet of water. Modern deepwater wells and operations generally occur in water depths of 5,000 feet or more. Ultra-deepwater wells can be drilled in water depths of 10,000 feet or more. The current record is for a well drilled in 2016 in more than 11,000 feet of water. Compare that depth to the tallest building in the world, Burj Khalifa in Dubai, which stands at 2,717 feet. It would take more than four of those buildings to fill 11,000 feet of water!
Deepwater hydrocarbon reserves could amount to nearly 350 billion barrels of oil equivalent. This is 8% of the earth’s hydrocarbon reserves. A barrel of oil equivalent, or BOE, represents the amount of energy in a single barrel of oil, which is approximately 1,700 kilowatt-hours of energy. The quantity of natural gas or other hydrocarbon that produces that much energy is a barrel of oil equivalent.
Further, two-thirds of those deep offshore oil and gas reserves have yet to be discovered!
Deepwater production is steadily growing, as well. Within two decades, deepwater production is expected to more than double, from 7.5 million BOE per day in 2015 to more than 18 million BOE per day by 2035.
However, these fields are highly complex, requiring specialized drilling techniques and equipment to overcome potential risk, ensuring wells are drilled safely without harming the environment or posing danger to crews.
Deepwater and ultra-deepwater reserves are found in several global basins. Deepwater hydrocarbons are particularly plentiful in the Gulf of Mexico, Brazil, Nigeria and Angola. The existence of significant deepwater resources along the east coast of Brazil and the west coast of Africa is no coincidence. It is due the phenomenon known as Continental Drift, a process that has occurred multiple times in the history of earth. This latest drift began some 200 million years ago, depositing a layer of salt that lies over massive oil and gas reserves.
The Gulf of Mexico is a huge energy resource for the USA. This map shows leases in various water depths in 2014. Companies bid competitively to the state or federal government to obtain these leases. During 2014, the US Gulf of Mexico supplied the US with 16% of its total oil and 4.5% of its natural gas, with deepwater fields contributing 82% of that oil and 54% of the gas.
The industry has a historically strong safety record when it comes to accidents that cause oil spills offshore, particularly relative to offshore production. In the 45 years from 1964 through 2009, 17.5 BILLION barrels of oil were produced in the Gulf of Mexico. During that time, 532,000 barrels of oil were spilled in federal waters as a result of “blowout” events, the uncontrolled release of hydrocarbons.
That’s point zero zero three percent of the oil produced during those 45 years. It represents about 30 barrels spilled for every million barrels produced.
However, the April 2010 Deepwater Horizon accident starkly showed industry that even stronger protocols and operational standards were needed for deepwater operations. Eleven workers died and 4.9 million barrels of oil were discharged into the Gulf of Mexico.
The industry’s response to the disaster was swift and sweeping, with the immediate formation of a joint industry task force and four panels focusing on equipment, operating procedures, subsea well control and containment and spill response. This rigorous, proactive call to action was undertaken to ensure such a disaster never happens again.
Since the event, the American Petroleum Institute has published more than 100 new and revised exploration and productions standards providing guidelines and best practices related to well design, worker training and well control equipment and containment, including the reliability of blowout prevention equipment.
Blowout prevention has been significantly improved through the American Petroleum Institute’s Standard 53, which was updated to standardize operating requirements, and added procedures for blowout preventer, or BOP, testing and routine maintenance.
To ensure greater safety in offshore drilling, the industry in 2011 established the Center for Offshore Safety.
Charlie Williams is the executive director of the Center for Offshore Safety: “The center of offshore safety is an industry association and we were set up because the industry wanted an organization like that but also because the presidential commission which recommended that there be a for the industry, by the industry, organization that was focused entirely on safety management and so center for offshore safety is that organization we have members but we're focused on helping the entire industry and every aspect of the industry. Contractors, marine contractors, drilling contractors, operating companies, big small and medium, so we run all kinds of events, most of our documents are available online and we run all types of events and forums and we encourage everybody to be there. We'll have panel discussions with smaller non-member companies, non-operator member companies and things like that at these events so that we can share the knowledge and improve the knowledge across the industry—but our main focus, our sole focus is safety and environmental management systems our focus is to have good auditing, have good audit tools and to gain good information and then to gain good information through other things like safety performance indicators and learning from incidents and taking that information and analyzing it to see where there is gaps and opportunities Our fundamental mission is to gain this information.”
A new, safety-focused federal agency, the Bureau of Safety and Environmental Enforcement, or BSEE, works with the industry to develop regulations related to well design, operational procedures and well control equipment, including BOPs.
One of BSEE’s most important offshore initiatives is the requirement that oil companies implement safety and environmental management systems, or “SEMS”, as a baseline of safety performance in order to remain active on the US Outer Continental Shelf. SEMS incorporates existing best practices for drilling, production, construction and well servicing and operations and requires E&P companies to cooperate with their third-party providers, including drilling contractors and service companies.
Said Mr Williams of the COS: Some people think about SEMs as being the same as process safety—process safety was a concept that came out quite a few years ago related to some chemical plant kinds of incidents that happened in the past. I think it's related to process safety, process safety is part of safety environmental management systems, I don't think it's the same thing, it is the same thing if you say your process is the entirety of what you do in any one location. If you say it's only about hydrocarbons flowing through equipment then I don't agree that process safety and SEMs are the same. So what is SEMs? What SEMs fundamentally is—it just says that you should have systematic way of managing everything you do on your developing your project and operating your project that delivers it in the safest possible way and so I always break it down—companies have had the SEMs idea for years and some companies have had really up and running systems for years, but people now that there’s been a huge focus on SEMs and there's been the auditing on SEMs, the companies that didn’t have them now have them, the companies that have them have learned a lot about them and how to even make them better.
Within months of the Macondo event, industry cooperated to provide advanced technology and response capability to a subsea well control incident, significantly expanding the reach of the US spill response network.
The Marine Well Containment Company, or MWCC, with ten members, who represent most of the deepwater wells in the US Gulf of Mexico Its mission – to be continuously ready in providing immediate response to a deepwater well control incident in the US Gulf of Mexico.
MWCC member companies have invested more than $1 billion – with a “B” – to ensure that any unplanned discharges can be quickly and efficiently shut off and the liquid captured aboard ships. MWCC owns all subsea equipment shown and has dedicated use of the modular capture vessels, used to contain flowing liquids from a well.
Each of the two containment systems, called Modular Capture Vessels, or MCV, is more than 161 feet tall, equivalent to the height of 12 stacked 18-wheelers. Each MCV is nearly 800 feet long, more than two football fields. Most importantly, this equipment can store up to 700,000 barrels of liquid, enough to fill 44 Olympic-size swimming pools. The liquid can be offloaded to smaller vessels for safe transport to shore.
The 30- to 40-foot subsea containment assembly is placed over a defective blowout preventer to contain the oil. The device can be broken down into two sections for easy handling, transport and installation when necessary.
Three capping stacks capable of handling pressures to a whopping 15,000 pounds per square inch are used either to cap the subsea well by creating a seal to stop the flow of fluid from the wellhead, or cap and flow the well by providing a channel to safely flow the fluids to vessels on the surface. The system is designed for water depths from 500 feet to 10,000 feet and temperatures as high as 350 degrees Fahrenheit.
Over the past six years, MWCC has worked with the BSEE and the US Coast Guard to develop a comprehensive system that combines state-of-the-art equipment and technology with a team of nearly 100 highly trained response experts, operating from two strategic locations along the Gulf Coast – Alabama and Texas.
In yet another initiative, the industry in 2013 established the Well Control Instituteto promote and encourage safe control well practices and well bore integrity through collaboration among operating companies, drilling contractors and service companies.
Say COS’s Mr Williams, “I think absolutely that we are the safest that we've ever been in the offshore. And I think the reason is — it's kind of a multifaceted reason, I think the first thing is the new spirit of collaboration and there's always been collaboration in the industry but I think the collaboration post Macondo horizon has been just an example of how the industry can really do it right and work together. So I think the working together has been really good and sustained and we worked on developing new standards that have impacted safety and new standards and practices and then we've worked on new systems that have improved safety like the subsea containment systems that have been worked on and deployed. And then of course we've worked on safety management systems themselves on SEMs and I think the dedication to those three things and the improvements that have been made have really improved and enhanced the safety. And I think the big thing that — lots of companies were doing well, in fact the industry had been doing well if you looked at personnel safety it's a tremendous success story. But I think what happened when we reflect back is that we didn't really have the right balance and we needed to really focus as much on safety management as we did on personnel safety, so I think that rebalancing and getting the right kind of focus on safety management and not allowing ourselves —we want great personnel safety but we want great safety management as well and I think that change and focus has really been important to improving safety in the industry and of course safety management systems focus on continuous improvement and continuous learning so they're not a one time event, they're a continuous event of having feedback and continuously improving what you're doing.”
With the industry’s continued commitment to rigorous operational standards and development of robust equipment, including well control equipment and new-age rigs outfitted with automated systems and sophisticated technology, the future for safe and environmentally responsible hydrocarbon production in deepwater and ultra-deepwater basins is brighter than ever. The wealth of oil and gas reserves in these new frontiers is significant, and one of the most important contributors to energizing the globe today and for future generations.