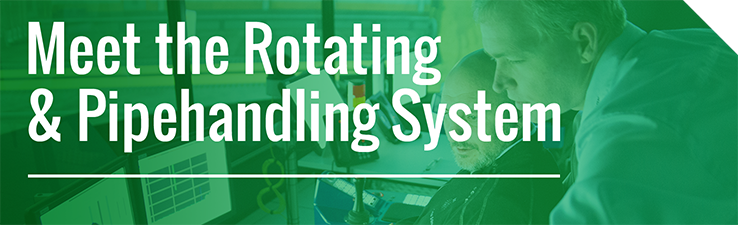
Meet the Rotating & Pipehandling System
Drilling wells requires the drilling rig to handle long, heavy strings of pipe and sophisticated electronic tools. It’s quite common for the hoisting system on drilling rigs to be capable of lifting as much as 2 million pounds, which represents more than twice as much weight as a Boeing 747 at take off. This module introduces the rig components designed to rotate and handle the drill string and bottomhole assemblies used to drill oil and gas wells.
A drilling rig is a complex piece of machinery designed for a single purpose — to drill oil, gas or geothermal wells.
Narration Transcript
Wells today are drilled by rotating a long string of pipe, the drill string, which is connected to a drill bit and additional tools at the bottom of the well. During drilling, the rig’s machinery always turns the pipe clockwise. Drillers call this “turning to the right”, which is also colloquial for “Everything’s A OK”.
Before the drill string can be rotated, however, the drill pipe must be brought aboard the rig and properly positioned in the derrick.
Very tall derricks are the most obvious clue that you are looking at a drilling rig. On large land rigs, derricks might stand more than 30 meters tall. In deepwater offshore drilling, some derricks are twice that height.
Derricks are tower-like structures with steel beams connecting all four sides, while masts are open on one side.
Masts can be lowered, disconnected and transported between locations, while derricks are less mobile. As a result, masts are more common on land rigs, which usually move frequently.
Derricks are generally found offshore, where they are permanently fixed to the drilling unit.
Both structures exist to support the weight of tools, pipe and devices that will be lowered into the well.
The power catwalk is designed to move tubulars, including drill pipe, from a horizontal position into the derrick near the well center. As the catwalk moves the drill pipe up into the rig, the drill pipe is seized by an elevator that moves the pipe into its proper position.
Elevators grip the pipe and can move it around the rig floor. There are various types of elevators for different applications. Elevators can be operated manually or hydraulically.
Once delivered to the rig floor, the rig’s pipehandling system can connect the tubulars into longer strings. This animation shows how the process can work offshore.
The longer strings are called “stands”. The most common type of stands are “triples”, which means three lengths of pipe joined together. Triples are roughly one hundred feet long, or about thirty-three meters. Building these stands in advance means that less time will be spent during the drilling process, which translates into more efficient drilling. The pre-built stands are then racked into the derrick’s pipe racks for later use.
In addition to triples, stands of two or even four lengths of pipe can be built. These are called “doubles and “fourbles”, respectively, and are less frequently used than triples. Some rigs use only single lengths of pipe.
The tubulars, which feature threaded connections, are connected and disconnected using an automated floor wrench, also called an Iron Roughneck. In drilling jargon, connecting pipe is called “make up”, while disconnections are “break out”. The automated floor wrench can also make up and break out drilling tools and drill bits, which also feature threaded connections.
In addition to making up and breaking out pre-built stands, the Iron Roughneck is also used to connect and disconnect drill-string tubulars as they go into and out of the well. A single crew member can control this machine with hand controls or automatic touch screens.
Regardless of stand size, the rig’s hoisting system moves the pipe over the rotary table for connection to other pipe already in the well.
The rig’s driller operates both the hoisting and rotating systems. On modern rigs, the driller controls these systems from an enclosed cabin, using joystick or touch-screen controls.
It’s quite common for the hoisting system on drilling rigs to be capable of lifting as much as 2 million pounds. That’s a lot of steel!
It represents more than twice as much weight as a Boeing 747 at take off! Lifting 2 million pounds takes a lot.
These large loads are applied to the derrick through the top of the mast, called the crown block. The drilling line is wire rope that is threaded through the stationary crown block and through the traveling block, which supports the drilling loads. Together, the crown and traveling blocks comprise a block-and-tackle pulley system.
The portion of drilling line extending from the drawworks to the crown block is called the “fast line”.
Moving loads up or down in the derrick is the job of the drawworks. It is the primary hoisting machine on a drilling rig. It also provides braking to stop and sustain weights imposed when raising or lowering drillpipe and drilling tools. Reeling in, or load raising, is powered by rig engines, while gravity powers load lowering, or reeling out.
The drawworks reel the fast line in and out. As noted, the fast line is reeled over the crown and through the traveling block. The other end of the drilling line, called the “dead line”, is anchored to the deadline anchor.
The top drive was introduced in 1982 and became a major enabler for non-vertical drilling. Powered by one or more electric or hydraulic motors, the top drive rotates the drill string clockwise – turning to the right
The top drive is suspended from a hook on the traveling block, which moves the top drive and the connected drill string up and down in the derrick.
A key benefit of the top drive is that it enables drilling with doubles, triples and fourbles. This greatly reduces connections while drilling, streamlining the drilling process.
Now that you’ve been introduced to the pipehandling and rotating systems, please meet the rest of the rig through the links on the “Meet the Rig” page.